Avoid Costly Mistakes: Common Hauling Issues Contractors Face
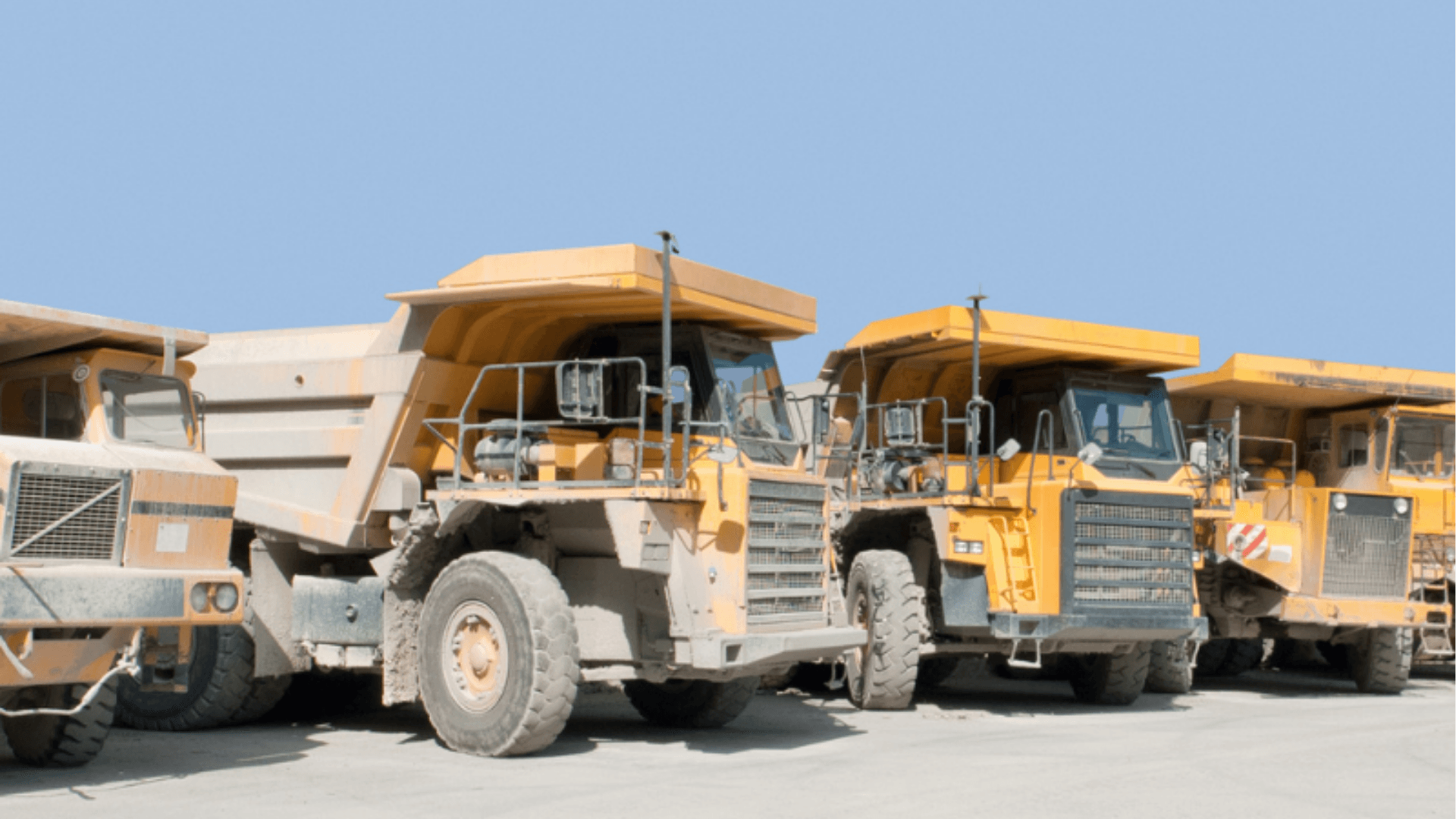
Miscalculating Material Quantities
Ordering the wrong amount of material, whether too much or too little, can seriously impact your bottom line. Over-ordering leads to material waste and on-site storage issues, while under-ordering forces project managers to scramble for additional loads, delaying the workflow.
How to avoid it:
✔️ Work with a hauler who understands material weights and load sizing.
✔️ Always confirm measurements and use weight-to-volume conversions when planning.
✔️ Build a reasonable buffer into your order, but avoid excessive overages that cost more in transportation and storage.
If your hauler isn’t confident estimating loads based on your specs, it may be time to work with someone who is.
Using the Wrong Type of Hauling Equipment
The wrong vehicle can damage materials, increase your trips, or slow down offloading. For example, certain stone or aggregate materials require covered or specialty trucks. Using a dump truck when a flatbed is better suited can also lead to material shifting or unnecessary breakage.
How to avoid it:
✔️ Match the truck type to the material. Ask your hauler about flatbeds, dump trucks, end-dumps, or specialty options.
✔️ Consider weather conditions that might affect fragile materials like topsoil or mulch.
✔️ Request your hauler’s recommendation for the best transport method.
A hauler with experience will offer equipment options tailored to your material—not just whatever truck is available.
Overlooking Compliance and Safety Regulations
DOT violations, improperly secured loads, and lack of proper permitting are not just risky, they’re expensive. Noncompliance can lead to rejected deliveries, legal penalties, and worksite shutdowns.
How to avoid it:
✔️ Partner with haulers who meet DOT and FMCSA safety regulations.
✔️ Ask for proof of permitting, load limits, and insurance before work begins.
✔️ Ensure drivers have valid CDLs and experience handling your specific load type.
Lack of documentation or unwillingness to answer compliance questions is a major red flag.
Hiring Based on Price Alone
Choosing the cheapest hauling provider often comes at the expense of reliability. Lower-cost haulers may use poorly maintained vehicles, lack insurance coverage, or have inconsistent scheduling.
How to avoid it:
✔️ Research the provider’s reputation, not just their rates.
✔️ Ask about equipment maintenance, past delivery performance, and communication standards.
✔️ Don’t sacrifice reliability to save a few dollars, an unreliable hauler often costs more in the long run.
A great question to ask before hiring: “How do you handle delays or breakdowns?” Their answer will say a lot about their preparedness.
The Bottom Line: Better Hauling = Better Projects
Avoiding these common hauling issues gives your project the best chance for success. From accurate ordering and equipment selection to compliance and reliable service, your hauling partner plays a key role in how efficiently your job site operates.
Choosing a hauling company that values accuracy, safety, and transparency can save you more than just money, it can protect your entire project timeline.
Conclusion
Material transportation is a cornerstone of successful construction, landscaping, and infrastructure projects. Addressing common challenges like scheduling, safety, and compliance ensures smooth operations and project success.
Facing Challenges in Your Material Transportation Process?
Discover how Commit Works Transportation provides reliable solutions to keep your project on track. Contact us today for a customized quote.
SEARCH
RECENT POSTS
CATEGORIES
Material Hauling & Logistics
Sustainable Transportation Solutions
Commercial & Infastructure Projects
Landscaping Material Hauling
Safety & Compliance in Transportation
Woman Owned Business & Leadership
Struggling With Material Transportation Challenges?
Download our free guide, The Complete Guide to Safe & Efficient Bulk Material Hauling, and gain expert insights to ensure smooth, reliable transport for your next project.
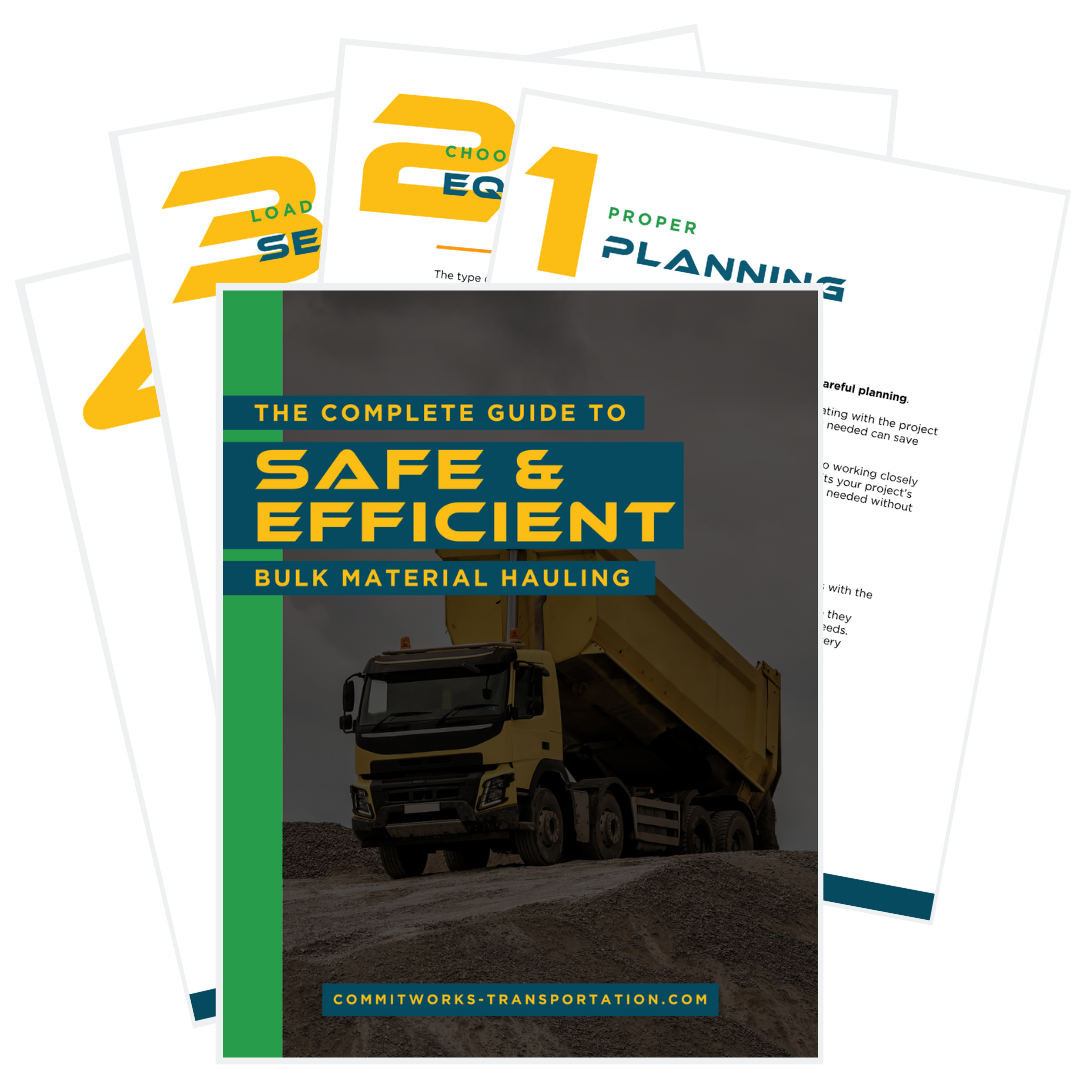